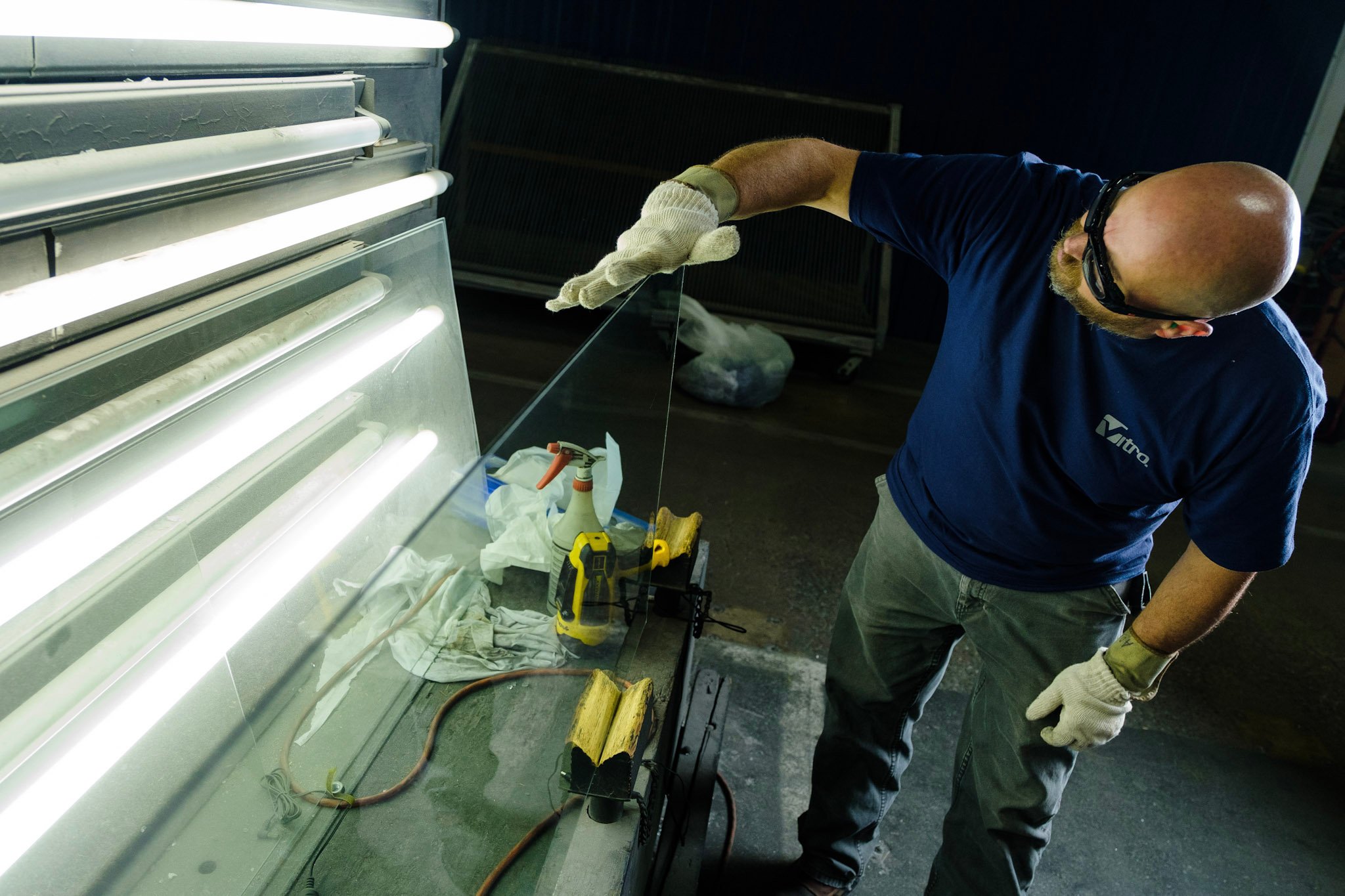
How We’re Optimizing Key Product Quality Indicators
The success of your business—and ours—hinges on product quality.
Over the past few years, Vitro Glass has made a concerted effort to raise our standards, monitoring a wide range of metrics that we call “Key Product Quality Indicators.” Below are two charts that demonstrate how we’ve improved quality to the benefit of fabricators in two critical areas in 2018.
The first quality indicator is credit performance. Simply put, this metric measures the volume of glass, measured in square feet, rejected and returned for credit by our customers each year. As you can see, after increasing steadily throughout 2015, 2016 and 2017, rejections have been dropping steadily through each quarter of 2018. During the most recent reporting period, we achieved credit performance levels not achieved since 2014.
Another key quality indicator that has seen dramatic improvement is the detection and prevention of void defects in our Solarban® coated glass products. These defects typically result from insufficient layer protection during the MSVD process or improper coating surface protection after the MSVD process.
As the second chart indicates, void defects have been reduced consistently throughout 2018. This success is the result of a specific internal void defect reduction initiative that encompassed the installation of new process monitoring equipment in 2017 and 2018 and the combined effort of staff assigned to the project from our research, engineering, production and quality control teams.
Working together, they continuously analyze coated glass returned by customers as well as product rejected internally through visual inspection and other quality control procedures. Using these defective materials, the team is translating the imperfections they record into increasingly sophisticated code for our quality control equipment, which has made it more effective at identifying defects and rejecting glass before it leaves our plants. The team also is using this feedback to strengthen our production processes.
The result is a continuous feedback loop that will enable us to refine and improve our manufacturing and quality control processes into the future.