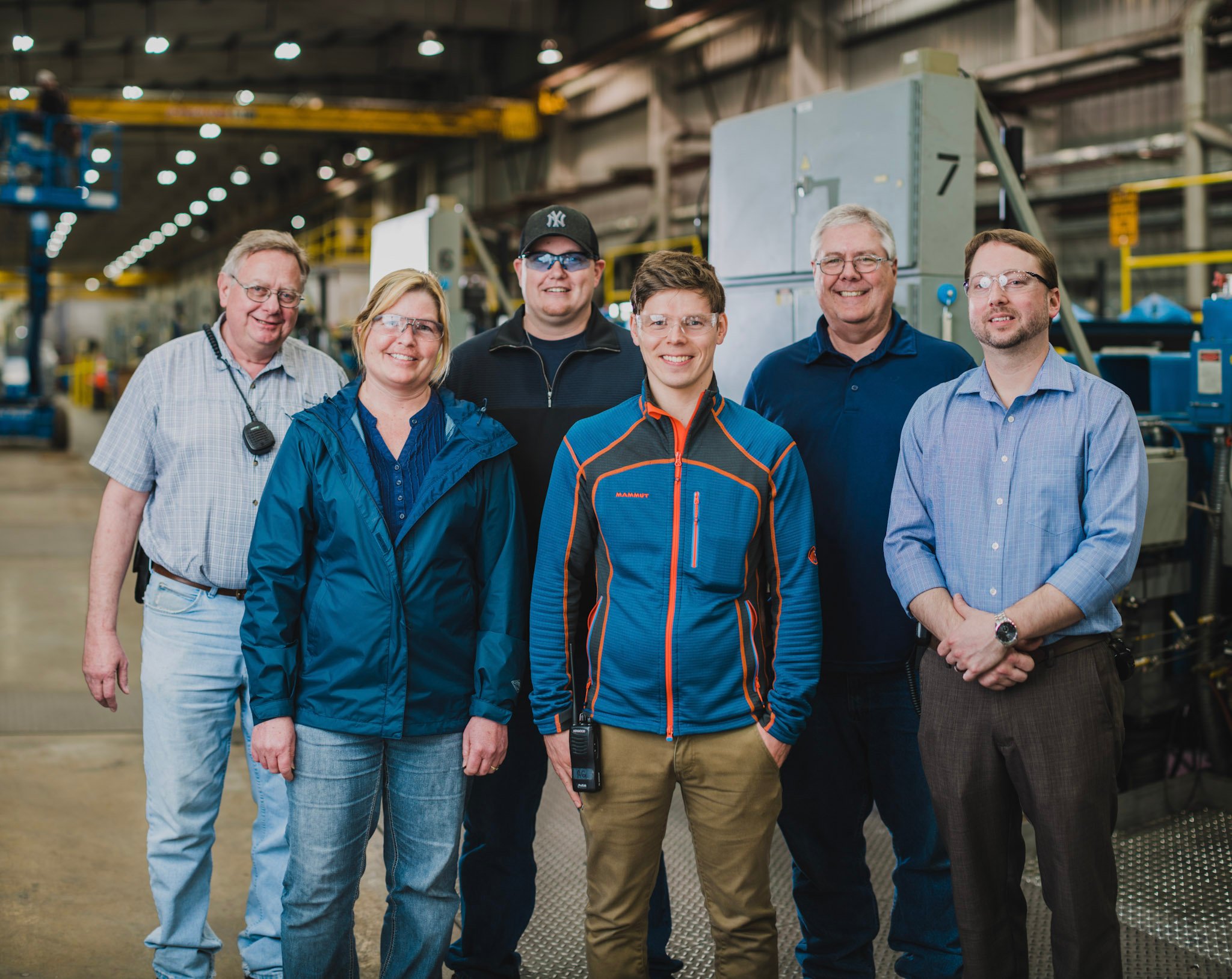
20 Years of Continuous Improvement
The Vitro Architectural Glass plant in Salem, Oregon, is a magnetron sputtered vacuum deposition (MSVD) glass coating facility that celebrated its 20th year of operation last year. Its 48 Vitro employees and eight contract workers are responsible for producing more than 50 million square feet of glass each year of mixed products, but can increase to upwards of 70 million square feet if only running double silver-based products.
The Salem plant is responsible for producing some of the most popular products in Vitro’s lineup, including:
- Solarban® 60 Glass
- Solarban® 60VT Glass
- Solarban® 70 Glass
- Solarban® 70VT Glass
- Sungate® 400 Glass
- Solarban® 67 Glass
- Solarban® 67VT Glass
- Solarban® R100 Glass
- Solarban® 90 Glass
- Sungate® 460 Glass
Salem is focused on continually improving its processes across production, inspection, and operations. “Our production focus has been on improving product quality and service reliability,” said Joe Terns, plant manager at the Salem plant. “We reduced downtime from 30.3 percent to 24 percent this year just by improving some of our basic maintenance practices. To improve the quality and efficiency of our inspections, we installed the ISRA visual camera system late last year and recently turned it on for auto rejecting,” said Terns.
Like all Vitro sites, the Salem plant is committed to environmental sustainability and community involvement. The plant has had a comprehensive recycling process in place for more than five years to recycle metal, plastic, banding, cardboard and electronics waste. Reuse and reduction is also a key initiative. “We cut our grass watering consumption by 70 percent and we’re planting natural drought-resistant vegetation with drip irrigation,” said Terns. “We also started a project to reuse our washer water and filter it into the cooling tower. We should save 35 to 40 percent of our production water usage when the project is completed.”
The plant just finished replacing facility lighting with LEDs that will pay for itself in less than 18 months. Salem’s energy sustainability team is currently working with the Oregon energy trust, and the plant is well on its way to saving more than 700,000 kWh this year.
Vitro’s Salem plant is active in the community as well. Their outreach team, led by Jeanelle Scott and Jaime Anderson, pick different causes each year, from charity runs to food toy drives to Salem educational support. “Last year we gave money to a science department and this year money for a science field trip,” said Terns. “We also use Garten Industries as a supplier that employs individuals with disabilities. We also have a part time beautification crew member who has disabilities and helps us to keep our plant safe and organized by keeping the plant clean and organized, managing our recycling and maintaining our environmental bio-swale area.”
The glass produced out of the Vitro Salem plant goes into some of the world’s most iconic buildings. Currently the plant is supplying the majority of the glass for the Singapore Changi Jewel Airport, which requires more than 500,000 square feet of Solarban® 70XL on clear glass.
It’s not Vitro’s largest facility, but the Salem, OR, plant is a vital component of Vitro’s increasingly more flexible and efficient glass production operations.